The Future of Aviation: 3D Printing Wings
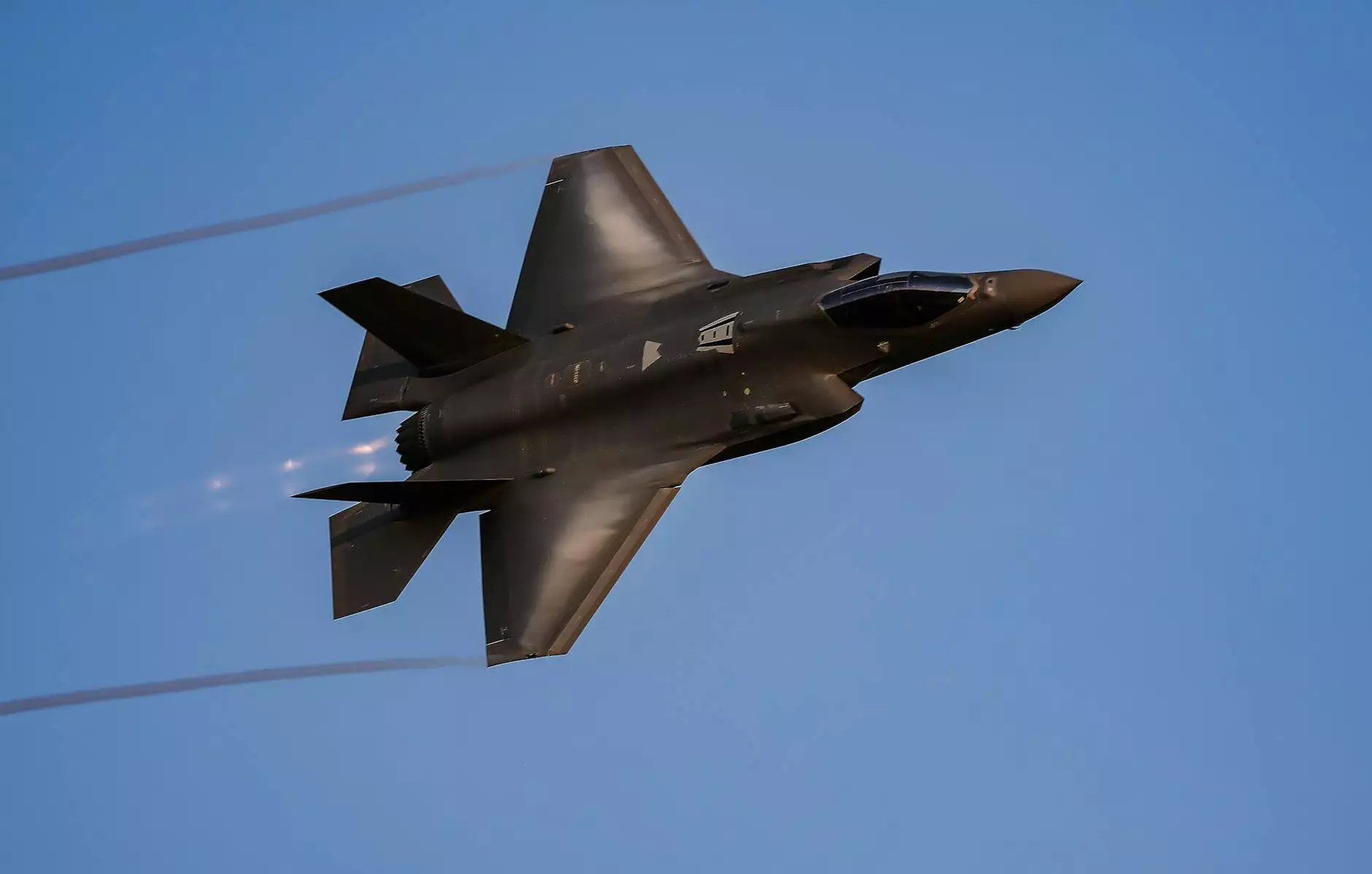
In recent years, technology has rapidly advanced, giving rise to 3D printing as a groundbreaking method in various industries, particularly in aerospace. One of the most significant innovations in this field is the development of 3D printing wings, which has the potential to revolutionize how we design and manufacture aircraft. This article delves into the intricate world of 3D printing wings, exploring its benefits, applications, and the future impact it holds for the aviation industry.
Understanding 3D Printing in Aerospace
3D printing, also known as additive manufacturing, is a process that creates three-dimensional objects layer by layer from a digital model. This innovative technique is transforming the aerospace sector by enabling the production of complex geometries that were previously unimaginable. The process allows for:
- Customization: Parts can be tailored specifically to meet the unique requirements of an aircraft.
- Reduction in Waste: Traditional manufacturing often results in significant waste, whereas 3D printing uses only the material necessary to create the part.
- Lightweight Structures: Essential for aircraft performance, 3D printing can significantly reduce the weight of components without sacrificing strength.
- Cost Efficiency: Over time, the decreased material waste and shorter production times can lead to considerable cost savings.
The Benefits of 3D Printing Wings
The innovation of 3D printing wings brings forth numerous benefits, enhancing both design flexibility and production efficiency. Below are some of the most compelling advantages:
1. Enhanced Aerodynamics
One of the main challenges in aviation design is achieving optimal aerodynamic performance. 3D printing allows designers to create intricately shaped wing structures that optimize airflow and minimize drag, thus improving fuel efficiency. This is crucial for the aviation industry as it leads to lower operational costs and reduced environmental impact.
2. Rapid Prototyping
The iterative nature of design in aviation necessitates quick prototypes for testing and validation. 3D printing wings enables engineers to construct working models in a fraction of the time it would take with traditional manufacturing methods, promoting faster innovation cycles.
3. Complex Geometries
Traditional manufacturing methods often limit geometrical complexity due to machining constraints. However, 3D printing technology enables the creation of complex, lightweight designs that enhance performance. This includes unique internal structures such as lattice designs that cannot be achieved using conventional techniques.
4. Supply Chain Optimization
By manufacturing parts on-demand, 3D printing wings can significantly reduce inventory costs and lead times. Parts can be produced as needed, streamlining the supply chain and reducing storage requirements.
Key Technologies in 3D Printing Wings
The advancement in 3D printing technologies has played a pivotal role in the development of wings for aircraft. Several methods cater to various materials and design requirements:
1. Fused Deposition Modeling (FDM)
FDM is a popular method in the 3D printing community. It works by melting thermoplastic filaments to construct parts layer by layer. While commonly used for prototypes, advancements in materials are making it increasingly viable for aerospace applications.
2. Selective Laser Sintering (SLS)
SLS uses a laser to sinter powdered material into solid structures. This method is particularly popular for producing durable and complex geometries, making it ideal for creating strong, functional wings that can withstand high-stress environments.
3. Direct Metal Laser Sintering (DMLS)
DMLS is a revolutionary method for metal parts and is becoming increasingly significant in aerospace applications. It allows for the creation of intricate metal wing structures, ensuring both strength and lightweight properties.
4. Continuous Filament Fabrication (CFF)
CFF is a relatively newer technology that combines traditional FDM with continuous fibers to enhance strength and thermal stability in printed parts. This method is promising for creating scalable wing components that require structural integrity under stress.
Applications of 3D Printed Wings
As the technology continues to mature, the applications of 3D printing wings within the aviation sector are vast. Here are some critical areas where this innovation is making a significant impact:
1. Prototype Development
Aircraft manufacturers can quickly create prototypes of innovative wing designs, enabling faster testing and validation to push the boundaries of what’s possible in aerodynamics.
2. Replacement Parts
3D printing allows for the on-demand production of replacement parts, minimizing downtime and ensuring that aircraft can remain operational with less need for maintaining extensive inventories.
3. Unmanned Aerial Vehicles (UAVs)
In the world of drones and UAVs, 3D printing wings allows developers to customize designs for specific missions, optimizing issues related to weight, flight time, and stability.
4. Experimental Aircraft
Innovative aerospace companies often push the envelope with experimental aircraft designs. 3D printing technologies enable them to test cutting-edge design concepts without the prohibitive costs associated with traditional manufacturing methods.
Challenges in 3D Printing Wings
While the benefits of 3D printing wings are overwhelming, several challenges must be addressed to achieve widespread adoption:
1. Material Limitations
Current 3D printing materials may not always meet the stringent performance requirements of aerospace applications. Research and innovation in composite materials and high-strength alloys are essential for overcoming this barrier.
2. Certification Issues
The aerospace industry is heavily regulated, and ensuring that 3D printed parts meet all safety and performance standards can be a lengthy process. Collaboration with regulatory bodies is crucial to streamline certification protocols.
3. Scale of Production
While 3D printing is excellent for producing individual parts, scaling up production for mass manufacturing presents challenges. Companies must find effective strategies for integrating 3D printing into existing production workflows.
The Future of 3D Printing in Aviation
Looking ahead, the future of 3D printing wings appears incredibly promising. As technology evolves, we can expect:
- Integration of AI: Artificial Intelligence will play a pivotal role in optimizing designs and automating the printing process, further enhancing efficiency.
- Advancement in Materials: Continued research will yield new materials tailored for 3D printing in the aerospace sector, likely making parts more durable and lightweight.
- Sustainability Focus: With an increased emphasis on eco-friendly practices, 3D printing can contribute significantly to reducing the carbon footprint of aviation through lightweight designs and efficient production.
- Global Impact: As more companies adopt this technology, we may see a shift in global dynamics within the aerospace industry, allowing smaller players to compete with established giants.
Conclusion
The integration of 3D printing wings into the aerospace sector marks a significant turning point in how aircraft are designed and manufactured. With its potential for enhanced performance, cost-efficiency, and rapid prototyping, 3D printing is not merely a passing trend but a vital component of the future of aviation. As challenges are addressed and technologies improve, companies like 3dprintwig.com will be at the forefront of this exciting evolution, leading the way toward a new era of aerial innovation.