Mig Power: Revolutionizing the Cutting and Welding Equipment Industry
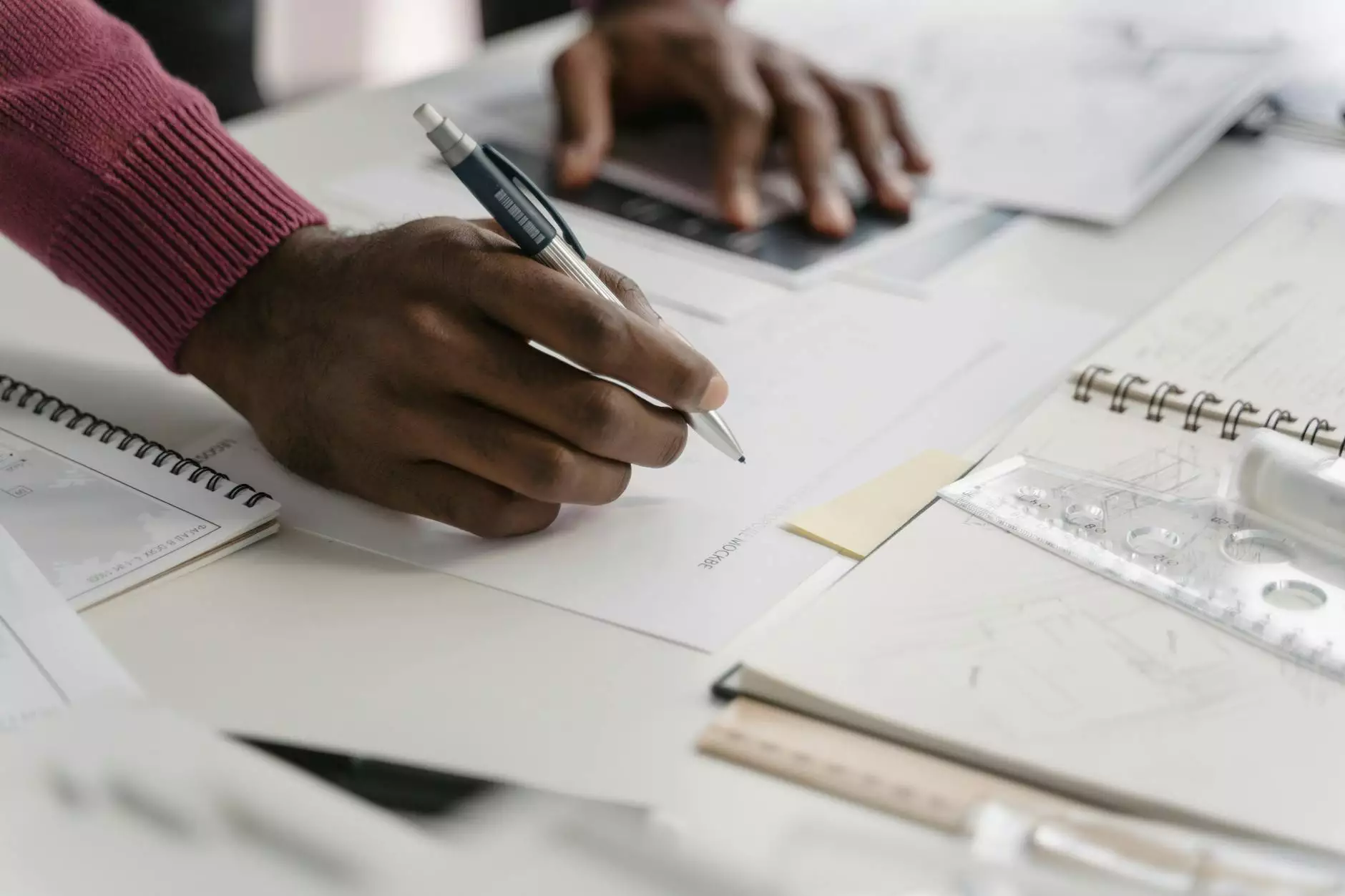
Mig power is a term that resonates strongly within the domains of welding and metalworking. It represents a state-of-the-art technology that has transformed the landscape of cutting and welding equipment. Companies like tiendaguve.com have leveraged this innovative approach, catering to a wide range of industries and applications. In this article, we will delve deep into the world of MIG power, its benefits, applications, and the future it holds for the welding industry.
What is MIG Welding?
MIG (Metal Inert Gas) welding, also known as Gas Metal Arc Welding (GMAW), is a welding process that uses a continuous wire feed as an electrode and a shielding gas to protect the molten weld pool from contamination. This technique has become one of the most popular methods in industrial applications due to its speed and versatility.
Components of MIG Welding
- Wire Feed System: The continuous feeding of a consumable wire electrode, which melts to create the weld.
- Shielding Gas: Typically Argon or a mix of Argon and Carbon Dioxide, this gas protects the weld from atmospheric contamination.
- Welding Gun: This tool feeds the wire and mixes it with the shielding gas before directing it onto the workpiece.
- Power Source: Supplies the necessary voltage and current for the process.
The Advantages of MIG Power in Welding
Understanding the advantages of MIG power is crucial for businesses looking to enhance their operational capabilities. Here are the key benefits:
1. Speed and Efficiency
MIG welding is known for its speed. Because it uses a continuous wire feed, welders can produce welds much faster than other methods, such as TIG or Stick welding. This increased efficiency translates to higher productivity, enabling businesses to meet demand swiftly.
2. Versatility
The MIG power technique can be used on a variety of materials, including steel, aluminum, and stainless steel. This versatility makes it an ideal choice for industries ranging from automotive to construction.
3. Ease of Use
MIG welding requires less skill compared to other welding methods, making it accessible for novice welders. The simplicity of the process ensures a shorter learning curve and faster integration into production environments.
4. Quality Welds
The continuous feed ensures that the weld pool stays consistent, leading to high-quality joints with minimal defects. Properly executed MIG welds are known for their aesthetic appeal and structural integrity.
5. Reduced Cleanup
Since MIG welding produces less spatter, the post-welding cleanup process is significantly less demanding than with other methods. This results in lower labor costs and time savings.
Applications of MIG Power
The applications of MIG power are vast and varied. From automotive repair shops to large-scale fabrication plants, this technology serves numerous sectors.
1. Automotive Industry
In the automotive sector, MIG welding is employed for chassis assembly, bodywork, and repair. Its speed and strength are essential for meeting the high demands of automotive manufacturing.
2. Construction Industry
MIG power is used in structural welding applications, where strength and reliability are paramount. This method allows for the quick assembly of frameworks and supports.
3. Aerospace Applications
The aerospace industry relies on MIG welding for projects requiring high precision and strength. The lightweight materials often used in aircraft can be effectively joined using MIG techniques.
4. Artistic Welding
Artists and sculptors also utilize MIG techniques to create metal sculptures, thanks to the fine control it offers and the aesthetic quality of the welds.
Future Trends in MIG Power
The future of MIG power in welding looks promising. As technology advances, we can expect the development of smarter and more efficient welding equipment. Here are some emerging trends to watch:
1. Automation and Robotics
Automated MIG welding systems are becoming more common. These systems can operate with high precision and consistency, reducing labor costs and increasing production rates.
2. Smart Technology Integration
With the rise of Industry 4.0, integrating smart technology into MIG welding processes will revolutionize quality control and operational efficiency. Real-time monitoring and data analytics will help optimize welding parameters and predict maintenance needs.
3. Eco-Friendly Practices
As industries become more environmentally conscious, advancements in MIG welding equipment will focus on reducing energy consumption and improving the recyclability of materials used.
4. Increased Safety Features
Future MIG welding machines are likely to incorporate enhanced safety features such as automatic shut-off, better ventilation, and improved ergonomic designs to protect the welder.
Choosing the Right MIG Equipment
Selecting the right cutting and welding equipment is critical for maximizing the benefits of MIG power. Here are some key factors to consider:
1. Welding Thickness and Material Type
Different machines are designed to handle varying thicknesses and types of materials. Ensure you select equipment that matches your specific needs.
2. Duty Cycle
The duty cycle is the amount of time a machine can operate continuously before needing to cool down. Consider your project requirements to select a machine with the appropriate duty cycle.
3. Portability
If your projects require on-site work, consider the portability of your MIG welding machine. Lightweight and compact models may be more suitable for fieldwork.
4. Features and Technology
Modern MIG welders may offer advanced features such as digital displays, automatic settings for various materials, and built-in safety measures. Invest in equipment that offers the latest technology for optimal performance.
5. Brand Reputation and Support
Choose reputable brands that offer reliable customer support and warranty services. This can provide peace of mind and ensure you have access to assistance when needed.
Conclusion
The impact of mig power on the cutting and welding equipment industry is undeniable. Its benefits in terms of speed, versatility, and quality makes it an essential technique for various applications. As technology continues to evolve, businesses leveraging MIG welding will likely see improved efficiency and reduced operational costs.
For companies looking to invest in cutting and welding equipment, focusing on tiendaguve.com can provide valuable insights and quality products tailored for today’s welding needs.
Embracing MIG power not only enhances operational capabilities but also prepares businesses for the future. As we move forward, staying abreast of industry trends and technological advancements will be crucial in maintaining a competitive edge.