Understanding the Power of **Die Casting** in Modern Metal Fabrication
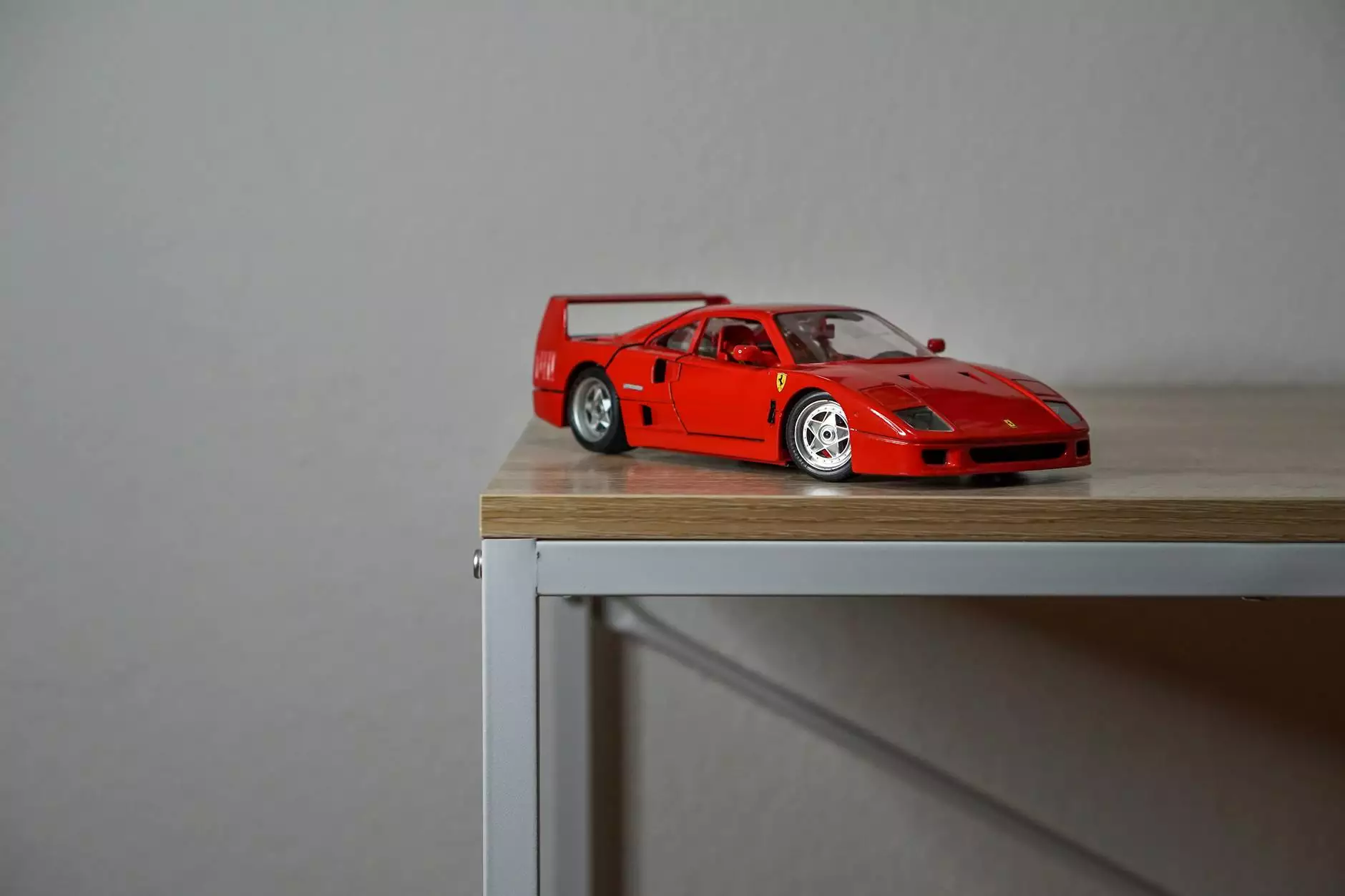
When it comes to metal fabrication, few processes are as essential and transformative as die casting. This article delves deep into the world of die casting, illuminating its methodologies, advantages, and diverse applications. As the industry continues to evolve, understanding this remarkable technique will empower businesses to harness its full potential.
What is Die Casting?
Die casting is a manufacturing process that involves forcing molten metal into a mold cavity under high pressure. This method is celebrated for its ability to produce complex shapes with high precision and repeatability. The molds, known as dies, are typically made from hardened steel and can withstand the rigors of high-pressure injection over extensive production runs.
The Die Casting Process Explained
The die casting process can be broken down into several critical steps:
- Preparation: The dies are cleaned and prepared to ensure optimal performance.
- Melting Metal: The metal, often aluminum, magnesium, or zinc, is melted at high temperatures.
- Injection: The molten metal is injected into the die at high pressure to fill the cavity.
- Cooling: The metal is allowed to cool and solidify within the die.
- Ejection: Once cool, the die opens, and the cast part is ejected for further processing.
- Finishing: Additional processes such as trimming, machining, or surface treatment may be applied.
Advantages of Die Casting
Embracing die casting offers myriad benefits that can significantly enhance manufacturing operations:
- High Precision and Detail: Die casting allows manufacturers to create intricate designs with tight tolerances.
- Cost-Effectiveness: Especially for high-volume production, die casting reduces material waste and labor costs.
- Durability: Components produced through die casting exhibit excellent mechanical properties, making them long-lasting.
- Versatility: With various metals and alloys to choose from, die casting caters to numerous applications.
- Rapid Production Rates: This method enables manufacturers to produce thousands of parts quickly.
The Different Types of Die Casting
Die casting can be primarily divided into two major types:
1. Pressure Die Casting
This method involves injecting molten metal into a mold at pressures ranging from 1,000 to 30,000 psi. This technique is typically used for non-ferrous metals like aluminum and zinc.
2. Vacuum Die Casting
In vacuum die casting, the air is evacuated from the die before injecting molten metal. This technique minimizes defects and improves the quality of the cast parts.
Applications of Die Casting
The versatility of die casting has led to its widespread adoption across various industries, including:
- Aerospace: Components such as engine parts, brackets, and housings.
- Automotive: Engine blocks, transmission cases, and structural components.
- Consumer Electronics: Housings for devices like mobile phones, laptops, and appliances.
- Medical Devices: Precision components that require strict adherence to quality standards.
- Furniture Hardware: Decorative and functional fixtures used in home and office furniture.
Future Trends in Die Casting Technology
The landscape of die casting is continually evolving, influenced by advancements in technology and methodologies. Several trends are shaping the future of this manufacturing process:
1. Automation and Robotics
The integration of automation and robotics into die casting operations is enhancing production efficiency, reducing labor costs, and minimizing human error.
2. Eco-Friendly Practices
With growing environmental concerns, many manufacturers are adopting sustainable practices, such as recycling scrap metal and reducing energy consumption during the die casting process.
3. Advanced Alloys and Materials
Innovations in metal alloys are expanding the application potential of die casting, enabling stronger, lighter, and more durable components.
Choosing the Right Die Casting Partner
Selecting a reliable partner for your die casting needs is crucial for the success of your projects. Here are a few factors to consider:
- Experience: Look for a company with a proven track record in the die casting industry.
- Quality Assurance: Ensure they adhere to strict quality control measures and certifications.
- Technological Capabilities: Assess their capabilities in utilizing advanced technology and automation.
- Customer Service: Choose a partner who offers excellent communication and support throughout the production process.
Deep Mould: Your Trusted Die Casting Partner
At Deep Mould, we specialize in providing top-notch die casting solutions tailored to meet the diverse needs of our clients. Our commitment to quality, precision, and customer satisfaction sets us apart in the metal fabrication industry.
Why Choose Us?
- Expert Team: Our skilled technicians and engineers are dedicated to delivering the highest quality products.
- State-of-the-art Equipment: We leverage the latest technology and machinery to ensure efficiency and accuracy.
- Custom Solutions: Whatever your project needs, we can provide tailored solutions to fit your specifications.
- On-time Delivery: We understand the importance of deadlines and strive to meet all project timelines.
The Bottom Line: Embracing Die Casting for Business Growth
In conclusion, embracing die casting is pivotal for businesses looking to enhance their manufacturing processes. The advantages, coupled with the ability to produce complex and durable parts efficiently, make it an invaluable technique in modern metal fabrication. As technology continues to advance, those who adapt and innovate with die casting will undoubtedly lead the charge in their respective industries. Partnering with an expert like Deep Mould can set you on the path to success in your manufacturing endeavors.
Invest in your future with die casting technology and watch your business thrive!