The Ultimate Guide to Choosing a Bottle Label Applicator
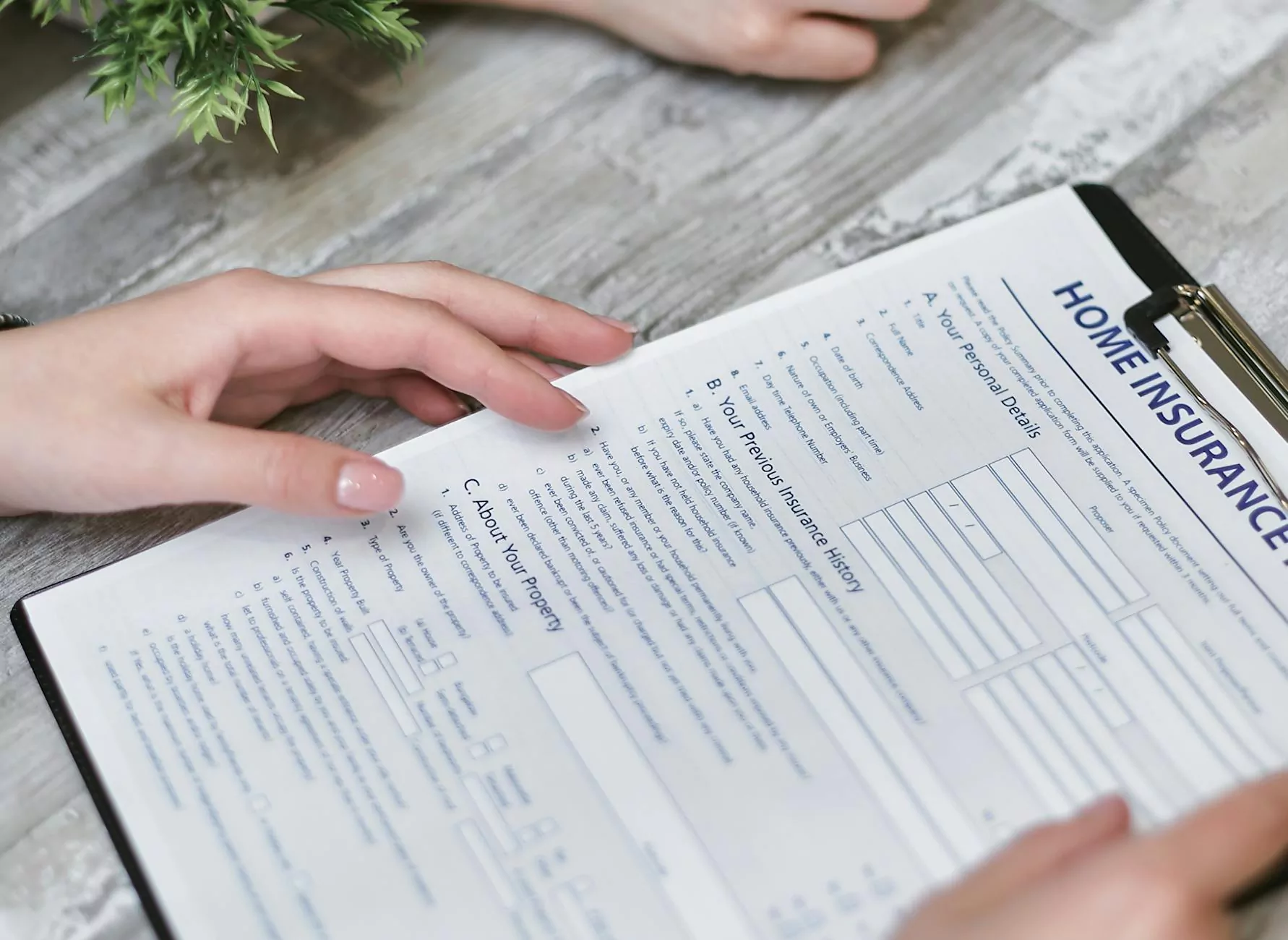
Businesses today face numerous challenges in maintaining efficiency and enhancing brand visibility. One of the most essential tools that can help achieve these objectives is a bottle label applicator. In this article, we will explore the significance of bottle label applicators, how they work, and tips for selecting the right one for your business needs.
What is a Bottle Label Applicator?
A bottle label applicator is a machine designed to apply labels to bottles quickly and accurately. Utilizing this automated tool can tremendously streamline operations, saving time and reducing labor costs. Whether your business deals with beverages, pharmaceuticals, or cosmetics, a reliable label applicator can enhance your packaging process.
The Importance of Labeling in Business
Labeling plays a crucial role in the marketing and operational efficiency of products. Here are some reasons why proper labeling is vital:
- Brand Recognition: Well-designed labels contribute to brand identity, making products easily recognizable to consumers.
- Regulatory Compliance: Many industries require specific information on labels for health and safety regulations.
- Informative Content: Labels convey important details about the product, including ingredients, usage instructions, and expiration dates.
- Marketing Strategy: Effective labeling can attract consumers and convey a brand message or story.
How Does a Bottle Label Applicator Work?
A bottle label applicator operates by using various technologies to accurately place labels onto bottles. Here's a breakdown of the process:
1. Label Design and Printing
Before labeling, your design must be printed, using a quality printer that ensures high-resolution text and images. Common printers for labels include inkjet, laser, and thermal printers. The choice depends on the type of material and printing volume.
2. Bottle Preparation
Bottles should be clean and dry prior to labeling. Any residue or moisture can affect the adhesion of the label, leading to a poor-quality finish.
3. Label Application
The applicator feeds the label from a roll, aligns it with the bottle, and applies it using one of several mechanisms, such as:
- Pressure-sensitive adhesives: These labels stick when pressure is applied.
- Heat shrink: These labels shrink tightly around the bottle when heated.
- Wet glue: A liquid adhesive applied to one side of the label.
4. Quality Control
It's important to implement quality control checks to ensure labels are applied correctly and are free from bubbles or misalignment.
Benefits of Using a Bottle Label Applicator
The incorporation of a bottle label applicator offers numerous benefits for businesses:
1. Increased Efficiency
Manual labeling can be time-consuming and prone to human error. Automated applicators can apply labels much faster, significantly increasing throughput.
2. Cost Savings
By reducing labor costs and minimizing waste through accurate application, businesses can achieve substantial savings. There is also less need for rework due to improper labeling.
3. Consistency and Accuracy
Automated machines deliver uniform results, ensuring that each bottle receives the same label placement every time, which is crucial for brand consistency.
4. Enhanced Professional Appearance
Labels that are applied smoothly and evenly enhance the product's professional appearance, contributing positively to consumer perception.
Choosing the Right Bottle Label Applicator
Selecting a bottle label applicator involves considering several factors to ensure it meets your operational needs.
1. Volume of Production
Assess how many bottles you need to label in a given time period. Some machines handle low-volume production, while others are specifically designed for high-speed applications.
2. Types of Bottles
The shape and size of your bottles will determine which applicator is suitable. Applicators can be designed for rounds, square, and even custom-shaped bottles.
3. Label Materials
Different applicators can handle various label materials such as paper, plastic, or eco-friendly options. Make sure the chosen applicator is compatible with your labels.
4. Automation Level
Determine whether you need a manual, semi-automatic, or fully automatic machine. Fully automated machines provide the highest efficiency but can be more expensive.
5. Budget Considerations
Pricing will vary based on the technology, brand, and capabilities of the applicator. Create a budget and select an option that balances cost and functionality.